Metallurgy
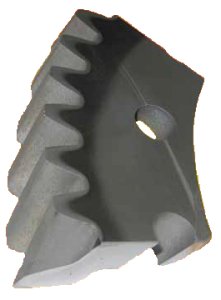
The Metallurgy Department was a single storey establishment, facing onto Maxey Road, sandwiched between the Heat Treatment Shop and the buildings that fronted onto Plumstead Road.
In the late '50s, it was manned by the very senior, and much respected, Mr W (Bill) Eaton and one technician.
The prime functions of the department were to monitor the quality of each batch of heat-treated parts, and to check and maintain the concentration of the cyanide baths, used to case harden small components.
Measuring the case hardening depth involved the careful use of water-cooled cutting wheel to remove a segment from, for instance,
a gear wheel, and then cut a section through a few of the teeth (as shown in the picture).
The sample was then moulded into a circular plastic mount, to hold it, before being ground and polished to a fine finish.
After being acid-etched, the case hardening layer would be revealed, and its depth measured with a calibrated microscope.
On meeting the design specification for the particular part, that batch of components would then be passed on for the next operation.
The only direct production operation performed in the Metallurgy Department was local hardening (and annealing) of certain areas of small components, the ends of clutch pushrods being an example, on an induction heat treatment machine.
.jpg)
This device consisted of a metal cabinet, housing electrical equipment that supplied high-frequency alternating current to a water-cooled,
hollow copper coil that protruded from the front of the machine.
Items to be heated would be placed centrally within the spiral-shaped coil and, when a foot pedal was operated, a timed sequence would be initiated
that induced an alternating magnetic field in the workpiece, the resulting eddy currents causing its outer surface to heat up.
If hardening of the item was the objective, then the timing would be set to allow the surface to heat up beyond its transition temperature,
after which the part would be removed from the coil and quenched in a suitable medium; oil or water.
If, however, local tempering or annealing of the part was required, then the cycle time would be adjusted to suit and, at the end of the
process, the part would be removed and allowed to air-cool.
Note: Any non-metallic objects (such as a finger) placed inside the coil were supposedly not affected by the electrical currents, but if the finger had a ring on it, that was a different matter!!
Later, in the early '60s, all the above sample testing and induction treatment work was undertaken by the Heat Treatment Shop itself, with the work usually reserved for the apprentice at the time, under the instruction of the shop foreman.
You can read more about the various metals used at AMC by clicking the following link.
W (Bill) Eaton | Chief metallugist | |
Don Hewitt | 1940 - 50 | Chief metallugist |