Grinding
.jpg)
Many motor cycle components, especially those from the engine, need to have a superior finish or tighter tolerance to that which can be achieved by turning or milling.
For this reason, grinding is an important process, without which interchangeable parts and low friction movement would not be possible to achieve.
A good example of both of these requirements is the crankshaft assembly shown here.
High surface finish and dimensional accuracy are needed for the big-end journals, against which the con rod shell bearings run, whilst both the crankshafts need to be of a tight tolerance to achieve the correct fit of bearings, sprockets and other components mounted on them.
The grinding bay at AMC was located on the ground floor, between the heat treatment shop and the press bay.
.jpg)
It was equipped with a full range of grinding machine types:
External - for crankshafts, camshafts, and other multi-stepped cylindrical shafts,
Internal - for sizing the bores of gears and parts requiring tight tolerances,
Centreless - for long, plain shafts and front fork tubes and
Surface - for assorted parts needing to be sized-up on their flat faces.
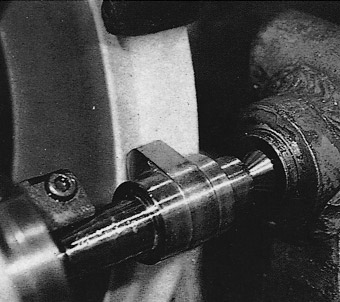
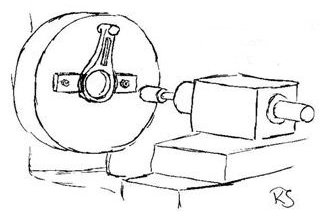
The grinding wheels for the external and centreless machines were quite large, over 600mm (2 ft) in diameter, and had to be accurately dynamically balanced to avoid vibration and possible fracture when running at high speed.
Those used on the internal machines were much smaller, as they had to do their work in the bores of the components.
In both cases, though, each wheel had to be "dressed" before and between operations by trimming its surface with a diamond-tipped tool. This ensured that any uneven wear and loss of material was counteracted for.
In the case of surface grinding, steel components were sometimes secured in position on magnetic plates.
Smaller machines used permanent magnetic plates but the larger ones usually had electro-magnetic versions which, in the event of a power cut whilst in operation, could result in a dangerous scattering of work parts from the machine.
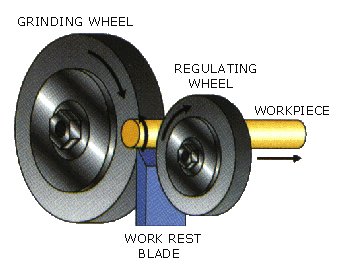
Centreless grinding was used for parts that needed their complete outside diameter finished to fine limits, a good example being the front telescopic suspension inner tubes.
For such long components, it was necessary to have two operators per machine, with one feeding in the workpieces and another removing them after having passed through the grinder.
The self-acting feed effect was produced by slightly canting the rubber-lined regulating wheel relative to the plane of the grinding wheel.
[Heavyweight boxing champion Henry Cooper uncovered some teething problems with this process, which you can read about in Henry Cooper at AMC.]
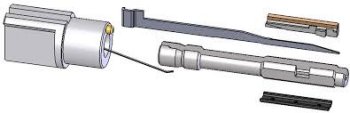
One other piece of equipment found in the grinding bay was an internal cylindrical honing machine, which was used to produce ultra-high finishes and tolerances in the small bores of items such a valve rocker arms.
In this process, the workpiece would be manually held, and slowly oscillated, over a rotating mandrel that was fitted with a spring-loaded strip of abrasive stone, whilst being lubricated by a stream of oil.
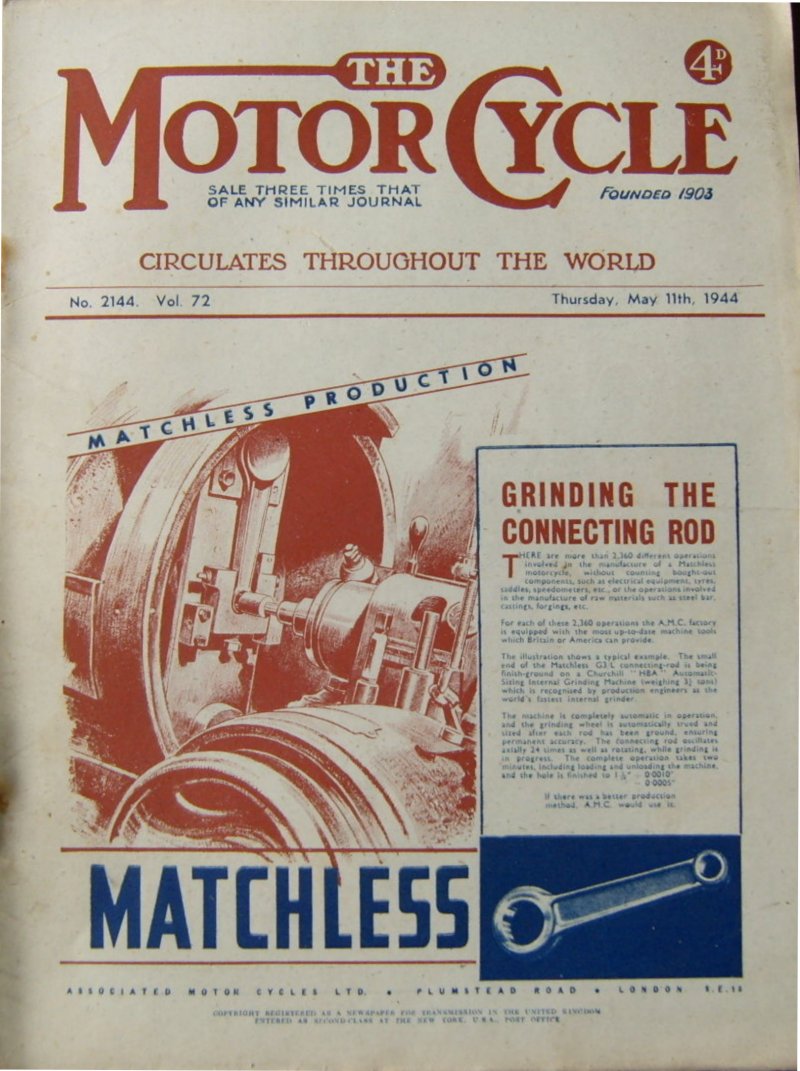
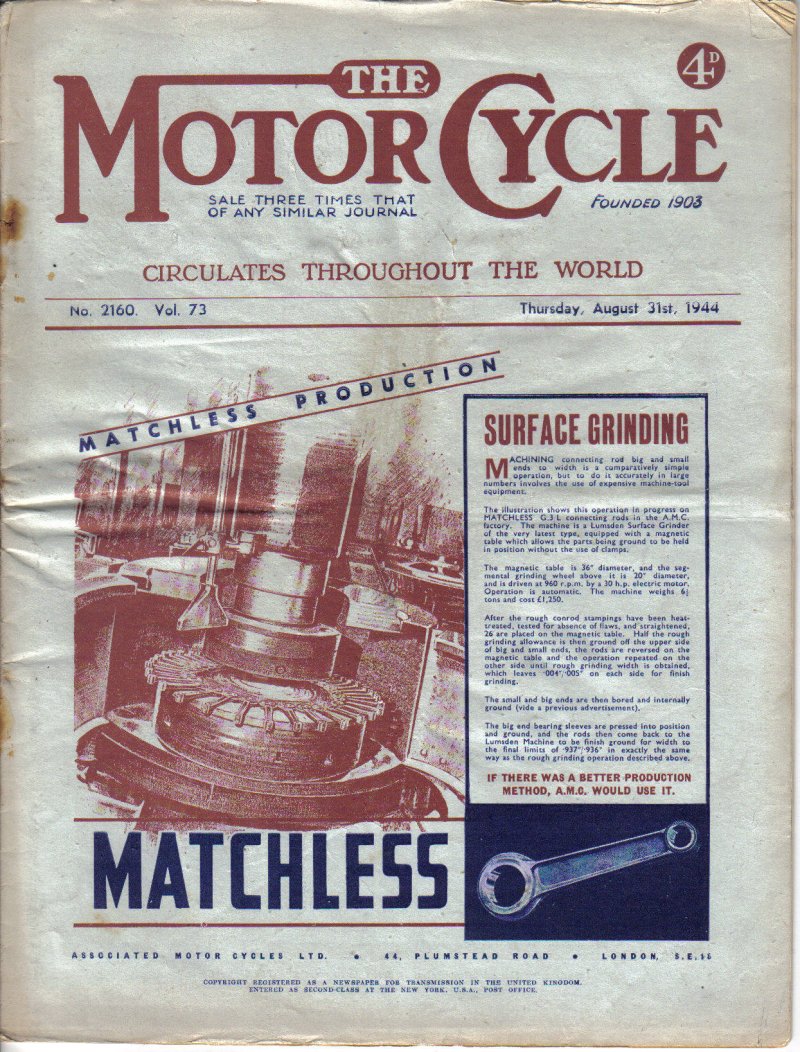
These two Motor Cycle magazine cover pages feature work carried out in the grinding department.
(Click on the images to see enlarged views)
You can view the complete collection on Cover Pages.
John Rourke spent over 30-years of his working life at AMC, some of it in the grinding bay.
You can read about his time there on Pages 17 and 21-24 of
'Memories of Plumstead'.
Fritz Appler | ||
Ray Burton | ||
Frank Carswell | Setter | |
Harry Coverly | ||
Peter Green | ||
Harry Moore | Setter | |
Jack Perkins | Foreman | |
John Rourke | (1928 - 61) | (dates incl. time in Drilling, Heat Treatment, Inspection and other departments) |
Peter Sands | ||
Geoff Woodward |